Core Technology
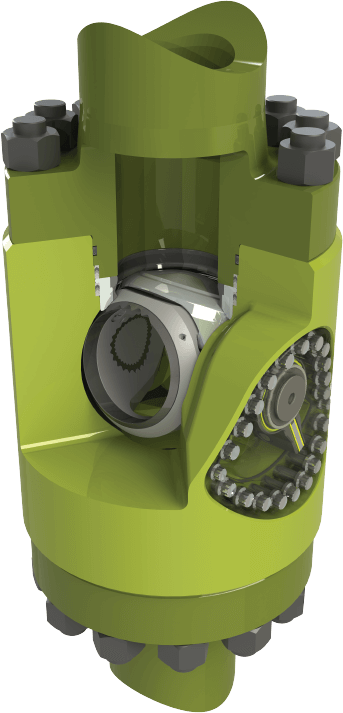
Shear and seal capability
Subsea intervention is reliant on the use of shear and seal valves to provide a critical safety barrier in the event of an emergency. These valves rapidly cut through well intervention media such as slickline, e-line, braided cable and coiled tubing and seal the wellbore to prevent hydrocarbon release.
Traditionally the industry has relied on three types of shear and seal valve: the ball valve, the gate valve and where space permits, the shear ram. Ball valves are usually arranged in multiples or stacks for confidence and cut with the same leading edge that is then required to create a seal. Many valves use projecting external actuators which can add a large amount of space, weight and cost and rely on elastomer components.
Differentiation
The Revolution valve uses separate components to cut and seal, with a gap between them, so that as the sealing element moves into place it does not drag over the cut edge of the obstruction, thereby maintaining its integrity and reliability.
Primary seals are manufactured from a high performance thermoplastic material with outstanding temperature, life and gas service performance.
Optimised cutting edges provide the hardness, strength and sharpness required to repeatedly cut various media types. Stiff components ensure that the edges cannot deflect and that the device is able to maintain an optimised, close shearing action with no risk of allowing media, particularly fibrous braided material, to lie across the seat.
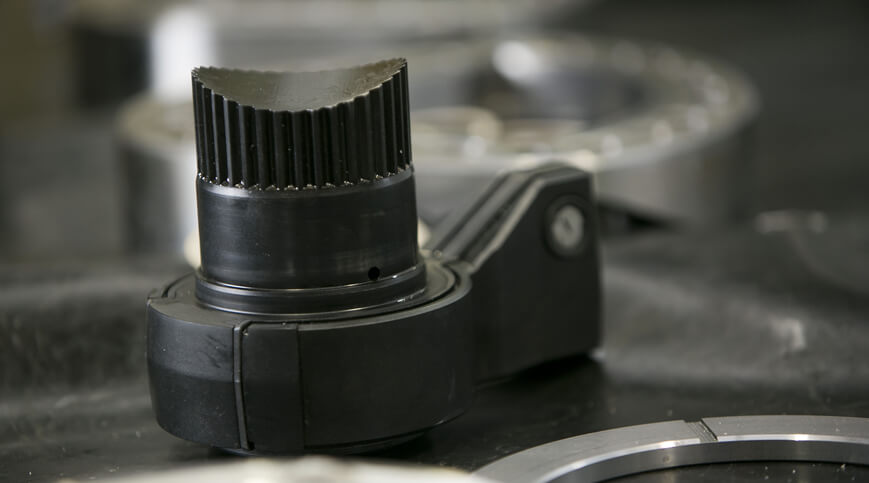
Power Delivery
The valve uses two fractional turn rotary actuators which are located on either side of the body and directly connected to the saddle via stout torque shafts. They are uniquely able to generate exceptional forces and facilitate superior cutting performance, requiring a much reduced amount of hydraulic fluid (1.5 litres). By locating the actuators on the outside of the device, the hydraulics are separated from the wellbore fluids. This ensures that the actuator seals operate in only a clean environment and the reliability of the device is significantly improved.
During development testing, the Revolution valve repeatedly cut multiple samples of slickline, braided cable and coiled tubing and has performed over many hundreds of cycles to confirm the device as an effective and superior solution.
The Revolution valve can cut intervention media up to and including 2” outer diameter, 0.203” wall thickness, 147 KSI tensile strength coiled tubing and can operate in deep water, high pressure, high temperature environments, exceeding the capability of all other comparable products on the market. Its compact design, through the use of its rotary actuators, means it can be used in in-riser and slim-line open water interventions.
Control system requirements for the valve have also been simplified, as the pressure rating of control lines is de-coupled from the pressure rating of the valve. This enables low cost, off the shelf components to be used for even 15,000psi or 20,000psi rated valves.
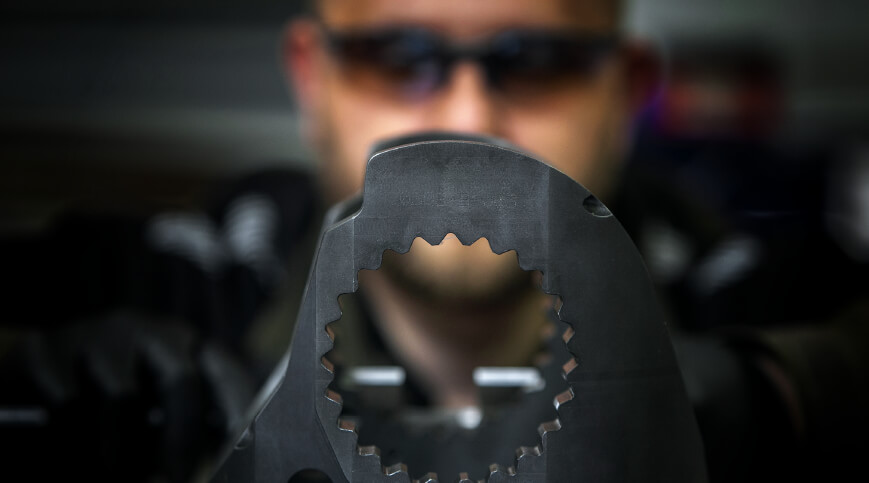
Reducing Cost
Overall, the Revolution valve uses fewer, simpler components and these are combined to produce a robust, fit for purpose, low maintenance product with significant benefits.
Historically, the cost of ownership for this class of device has been a material consideration, as frequent and expensive maintenance was required to ensure equipment readiness. The Revolution valve can be assembled quickly and does not require any specialist tooling or extensive training or knowledge.
The design itself is efficient and can be manufactured economically using basic oilfield, low alloy steel material for all major structural components.
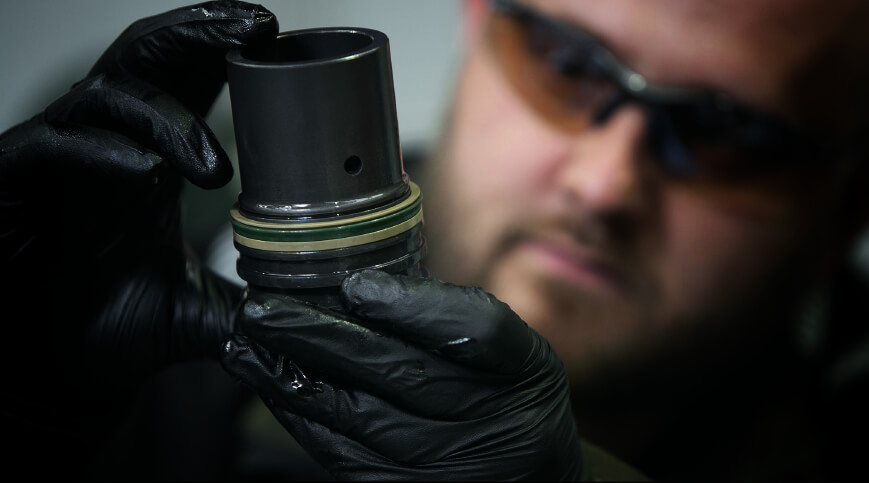
The Future
With an industry drive for increased production, a greater operational range of well depths and bore sizes and increasingly stringent safety standards, the demands on safety valves have increased exponentially. It can be argued that existing solutions are approaching their technical limit, so a whole new approach is required to address these challenges.
Our Revolution valve has been designed to meet these challenges whilst reducing the cost of manufacture and ownership by around 50%. With its exceptional performance, it is the only solution on the market that has been able to surpass endurance testing over many hundreds of cycles and is specifically designed to meet the highly rigorous API 17G industry gold-standard.
The valve is a truly innovative and versatile arrangement with many applications. Its capabilities mean that it is suitable for use in surface intervention, subsea in-riser completion installation and intervention, open water well control package and EDP valves, abandonment tree saver valves (a compact lightweight tree-on-tree system for use during well abandonments to allow well access without overstressing the xmas tree), subsea lubricator valve assemblies or any application that requires a compact and robust shearing and sealing device.
Features
Benefits
Fewer, simpler components and stronger fit-for-purpose design
- Minimises cost
- Improves reliability
- Reduces lead time
Separates cutting and sealing components in a single device
- Eliminates risk of damage to the seal during cutting giving unparalleled post–cut sealing performance
Rotary actuators
- Eliminates binding and maximises cutting torque
External actuators
- Separates controls from the wellbore environment
- Ensures rapid closure
Resilient well bore sealing
- Enables use in high pressure and high temperature applications
- Provides explosive decompression resistance
- Enables use in high pressure and high temperature applications
Compact and lightweight design
- Facilitates installation in short BOP’s
- Allows additional or alternative valve functions to be incorporated
Common flanged connection
- Improves structural integrity including fatigue capacity
- Reduces cost
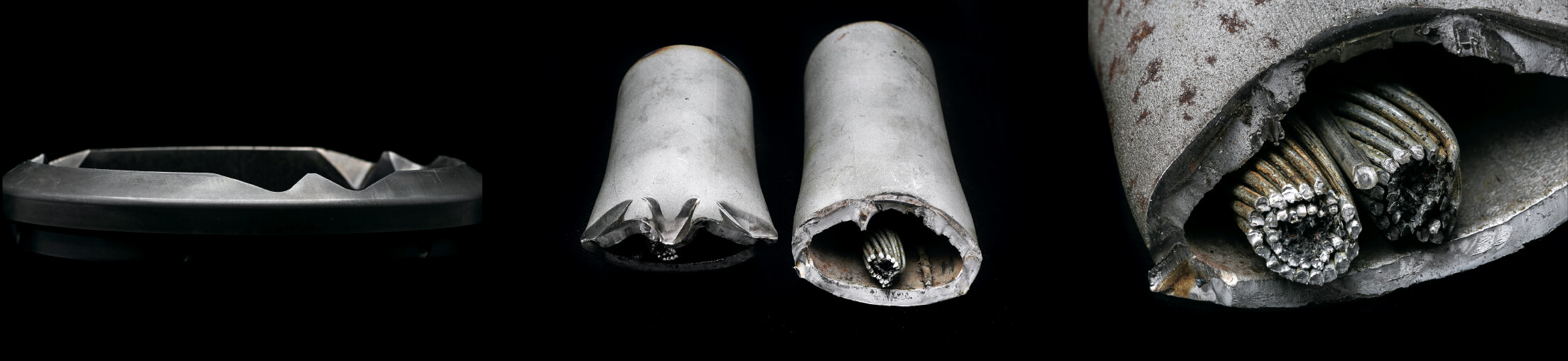